- What are the primary safety concerns associated with hydrogen in industrial and commercial applications?
- How is hydrogen leakage and fire detected with available technologies?
- What common sensing technologies are not applicable for hydrogen gas and why?
- How do hydrogen detection systems work, and what types are most effective?
- What are the standards and regulations that govern hydrogen safety and detection in various industries?
- How often should hydrogen safety systems be tested and maintained for reliable operation?
- What role does ventilation play in hydrogen safety in facilities?
- How have advancements in technology improved the effectiveness of hydrogen detection and safety systems?
- What should be considered for detector selection and placement?
Browse all hydrogen detectors from leading B2B suppliers on our marketplace!
What are the primary safety concerns associated with hydrogen in industrial and commercial applications?
As more industries turn to hydrogen as a clean energy carrier and a cornerstone of the hydrogen economy, it's critical to understand the associated hazards and implement robust hydrogen safety measures and systems. While hydrogen is safer in some ways than other fuels (as it disperses quickly in air and is non-toxic), it is still highly combustible, can cause hydrogen embrittlement, and is an asphyxiant gas. Its unique properties also pose special safety issues and hydrogen safety challenges. Specifically:
Hydrogen gas is not visible and has no odor, making it undetectable by human senses. Industry odorants may not be effective; many react with hydrogen or surfaces in the hydrogen storage and delivery system. Hydrogen can degrade odorants or cause interactions with other materials. High-purity hydrogen, often required for fuel cells and other hydrogen technologies, cannot tolerate impurities. Other hydrogen forms such as cryogenic hydrogen and liquid hydrogen need special handling. Hydrogen is lighter than air. In confined areas, it rises to ceiling level, displacing oxygen. However, hydrogen is difficult to detect in open spaces. Pressurized leaks can be hard to detect as the gas jet direction is unpredictable, making detector placement difficult. When mixed with air, hydrogen is highly combustible and can spread rapidly. A pure hydrogen flame is nearly invisible in daylight and fails to trigger traditional heat detectors. Liquid hydrogen poses extra risks like cryogenic burns and over-pressurization in hydrogen storage tanks. Managing ignition sources and controlling minimum ignition energy in hydrogen systems is critical. Hydrogen and air mixtures are particularly vulnerable to explosions.
How is hydrogen leakage and fire detected with available technologies?
Ultrasonic Gas Leak Detection (UGLD)
When pressurized hydrogen leaks, it generates ultrasonic sound. Monitors detect airborne ultrasound above a set level. A single detector can respond to even a small hydrogen leak, unaffected by wind direction. UGLD is ideal for monitoring pipes, hydrogen storage tanks, hydrogen fuel tanks, and vessels. Instruments can alarm quickly as ultrasonic noise travels at the speed of sound.
Point Catalytic Bead
With this detection method, gas enters the sensor and contacts pellistors. It’s oxidized in the presence of oxygen. A Wheatstone Bridge converts the resistance change into a sensor signal. These sensors are widely used in hydrogen safety applications, including facilities handling gasoline and alternative fuel systems.
Point Electrochemical
These sensors utilize a chemical reaction that generates a current proportion to the hydrogen concentration. The gas enters through a membrane; oxidation and reduction reactions create a measurable current. These sensors are particularly effective in detecting low hydrogen concentrations, such as those present in fuel cell systems and in the handling of liquid hydrogen.
UV/IR Hydrogen Flame Detection
These detectors monitor both infrared and ultraviolet radiation to detect hydrogen flames. When hydrogen burns, IR radiation is emitted by steam generated from combustion. An algorithm filters out false signals from hot objects and reflections. UV sensors detect deep UV radiation, and the combined IR/UV detection results in fast, reliable flame detection with reduced false alarms.
What common sensing technologies are not applicable for hydrogen gas and why?
Hydrogen is colorless, odorless, and transparent to IR radiation (unless burning). Infrared sensors detect IR light absorption by gas molecules, but hydrogen lacks a significant IR absorption band in the mid-infrared range. So, IR sensors are ineffective for hydrogen leak detection.
How do hydrogen detection systems work, and what types are most effective?
A system combining several hydrogen gas and fire detection layers can ensure reliable protection across plant layouts. Each detection type has advantages and limitations. Layers help prevent hazards from escalating. Modern hydrogen detection systems use a layered approach that mimics human senses. Ultrasonic sensors "hear" leaks, catalytic bead and electrochemical sensors "sniff" gases, and optical sensors "see" flames. These hydrogen systems connect to certified controllers that can execute safety actions during leaks or fires. They support energy goals including sustainable energy, renewable energy, and green hydrogen.
What are the standards and regulations that govern hydrogen safety and detection in various industries?
Fire and explosion are key safety concerns with hydrogen, especially with its wide flammability range of 4% to 77% in air. Explosion protection is governed internationally by IEC/EN/ISA 60079 and ISO/IEC 80079. Specific hydrogen safety standards include:
ISO 22734 - Hydrogen generators using water electrolysis — Industrial, commercial, and residential applications: requires manufacturers of electrolysers to perform a risk assessment. Depending on the final placement location of the equipment, plant owners/operators may need to perform their own additional assessment on the hydrogen generator, applying zone classification using IEC 60079-10-1 or an appropriate national standard.
ISO 19880 - Gaseous hydrogen — Fueling stations: requires that sites must be inspected in accordance with the IEC 60079-10-1 standard or sufficient national regulations. This includes zone classification and ignition protection methods to IEC 60079, ISO/IEC 80079 and NFPA 2.
The Center for Hydrogen Safety helps promote awareness and best practices. The Hazardous Materials Safety Administration regulates hydrogen energy systems and associated codes and standards. Journal articles also guide the evolution of safety practices.
How often should hydrogen safety systems be tested and maintained for reliable operation?
Routine maintenance of flammable gas detection systems is essential to ensure long-term reliability. Product manuals provide service guidance, and users can also refer to IEC/EN 60079-29-2 for best practices in selection, installation, use, and maintenance of gas detectors.
Maintenance frequency will depend on environmental conditions and system usage. However, systems with built-in self-testing can provide real-time diagnostics and alert operators when maintenance is needed.
Examples:
UGLD (Ultrasonic Gas Leak Detection)
The Observer® i by MSA features the Senssonic™ self-test function, checking electrical integrity and microphone performance every 15 minutes. This helps ensure consistent sensitivity and detection coverage.
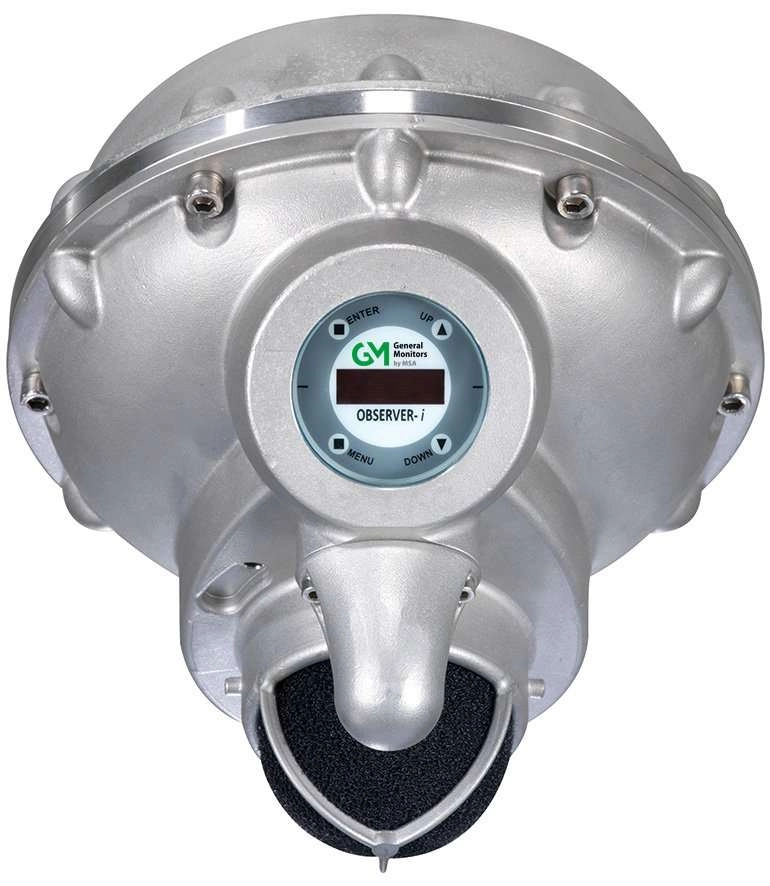
Flame Detectors
The FL500-H2 by MSA includes Continuous Optical Path Monitoring (COPM), checking the optical path and electronics every 2 minutes. If debris or other obstructions block the sensor for two consecutive cycles, the system activates a fault alert.

Proactive maintenance supported by intelligent diagnostics improves system performance and enhances hydrogen safety outcomes.
What role does ventilation play in hydrogen safety in facilities?
Ventilation and air movement serve two primary purposes according to IEC 60079-29-2:
- Enhancing dilution and promoting dispersion to limit the extent of hazardous gas areas.
- Preventing the persistence of explosive atmospheres that could influence hazardous area classification.
Ventilation rate must be evaluated against expected flammable gas leakage rates under different conditions. This assessment informs how ventilation and gas detection systems should work together. Detailed guidance can be found in IEC 60079-10-1, Annex B.
Integrated safety functions can include:
- Disconnecting non-explosion-protected equipment when gas levels exceed alarm thresholds.
- Increasing ventilation rates to prevent gas concentrations from exceeding safe levels.
ISO 22734 and ISO 19880 also outline requirements for ventilation as part of hydrogen production, storage, and distribution safety strategies.
How have advancements in technology improved the effectiveness of hydrogen detection and safety systems?
The latest generation of ultrasonic detectors feature Artificial Neural Network (ANN) algorithms to detect compressed hydrogen leaks. These algorithms use advanced sound processing to differentiate genuine gas leak sounds from background noise, referencing acoustic data collected over years from both onshore and offshore industrial environments. Compared to older detectors that only monitor frequencies above 25 kHz, modern systems can listen as low as 12 kHz, improving detection range while minimizing false alarms.
The Observer® i, which is MSA’s latest third-generation UGLD, requires no alarm set points or trigger levels to be configured, and no time-consuming “training” sequences before installation. For dependable operation, a patented self-test function, Senssonic™, runs integrity checks every 15 minutes. The unit provides accurate identification and detection of hydrogen gas leaks from 2 bar (29 psi) pressure, from distances up to 28 meters, at the speed of sound.
What should be considered for detector selection and placement?
Correct placement and the use of multiple detector types increase the chance of early hydrogen detection. Most detection setups rely on point gas detectors like catalytic bead and electrochemical sensors. However, these can be less effective in open or unconfined areas where hydrogen may escape as narrow, high-velocity gas jets.
Due to unpredictable leak directions and the high pressure involved, such gas jets may bypass detectors for extended periods. Therefore, it’s difficult to rely solely on point sensors for comprehensive coverage. Plume modeling and gas mapping software tools can show where traditional sensors may fall short and highlight the effectiveness of ultrasonic gas leak detection in comprehensive hydrogen safety planning.
Content contributed by
Founded in 1914, MSA Safety is a global leader in the design and manufacture of safety products that protect people, equipment and the environment. With a worldwide sales and service network, we equip international customers from all sectors of the oil and gas, petrochemical, fire, construction, mining, military, automotive, power generation and wastewater industries and many more. We equip your hydrogen project with the right gas and flame detection system for maximum protection against explosive, flammable and toxic gases.