- What is the main purpose of the manufacturing readiness level?
- Why is the manufacturing readiness level so important for hydrogen systems and components used in the hydrogen economy?
- What does a manufacturing readiness level of 10 (MRL 10) represent?
- What does a manufacturing readiness level of 9 (MRL 9) stand for?
- How is a manufacturing readiness level of 8 (MRL 8) defined?
- What is meant by a manufacturing readiness level of 7 (MRL 7)?
- What is indicated by a manufacturing readiness level of 6 (MRL 6)?
- What is indicated by a manufacturing readiness level of 5 (MRL 5)?
- What is inferred by a manufacturing readiness level of 4 or lower?
What is the main purpose of the manufacturing readiness level?
The concept “Manufacturing Readiness Level“ (MRL) is commonly used to describe maturity of production readiness for a specific product. Manufacturing process quality for an engineering product is generally achieved in different phases, starting with the first production designs and working towards a fully optimized production process as the final goal. In an effort to standardise across industries, several production readiness levels have been defined as a matter of convention for purposes of assessing production quality.
All products in the Hyfindr marketplace are categorized according to their manufacturing readiness level and a product search can be filtered using the MRL parameter.
Why is the manufacturing readiness level so important for hydrogen systems and components used in the hydrogen economy?
Many products in the hydrogen-based industry are not yet fully scaled up, given that production volumes have not yet risen to levels seen in other segments of the energy economy. Fuel cell engines and the components required to build modern-day hydrogen systems have not yet generated economies of scale currently existing in the conventional combustion engine or battery system domains. Within such framework conditions it is therefore of utmost importance for designers and engineers to know the production maturity of fuel cell components, both regarding the development level and the manufacturing level.
In an ideal scenario, one would design a fuel cell or hydrogen system comprised only of components with a technology readiness level of 9 (TRL 9) and a manufacturing readiness level of 10 (MRL 10). This would mean that the newly designed system, despite not meeting any such criteria as of yet, would at least in other respects consist of technology which has been tested in its operational environment, and is manufactured in series using lean production processes. The focus can now be on improving the quality of the newly designed system. Any testing of such system becomes much easier regarding root cause analysis. Some hydrogen system components can be adapted from other energy systems but in moving closer towards the actual fuel cell within the fuel cell system, components classified in the TRL 9 and MRL 10 categories are still a rare find.
The hyfindr.com marketplace makes life easy for engineers and purchasing professionals alike, by identifying product maturity and registering every product listing with its maturity level. Suppliers listing their products on the hyfindr.com marketplace commit to keeping such criteria up to date.
What does a manufacturing readiness level of 10 (MRL 10) represent?
A manufacturing readiness level of 10 (MRL 10) generally means that full-rate production has been demonstrated and lean production practices have been implemented. An organisation would need to be able to answer all questions below with “YES” in order to deserve this rating:
- Is the system, component or item in full-rate production?
- Have technologies matured to a technology readiness level of at least 9 (TRL 9)?
- Is this level of manufacturing normally associated with the production or sustainment phases of the acquisition life cycle?
- Does the system, component or item in full-rate production meet all engineering, performance, quality, and reliability requirements?
- Are all materials, manufacturing processes and procedures controlled according to Six Sigma (6σ) or another appropriate methodology for quality management? Does this also apply to the inspection and testing equipment used in production?
- Do unit costs for the rate of production meet the targets set, and is funding sufficient for production at the required rates?
- Are lean manufacturing practices well established and process improvements continuously ongoing?
What does a manufacturing readiness level of 9 (MRL 9) stand for?
A manufacturing readiness level of 9 (MRL 9) generally means that the manufacturing process has been validated. An organisation would need to be able to answer all questions below with “YES” in order to deserve this rating:
- Is the production line operating at the desired initial Sigma level?
- Is production output stable?
- Is the design stable, requiring few or no design changes?
- Are all manufacturing processes controlled using Six Sigma (6σ) or another appropriate quality management mechanism?
- Have affordability concerns been accommodated for initial production, and likewise for evolutionary acquisition milestones?
- Do cost estimates amount to < 110% of costing targets, or have costing targets been met (e.g. “design-to-cost” (DTC) targets achieved)?
How is a manufacturing readiness level of 8 (MRL 8) defined?
A manufacturing readiness level of 8 generally means that the maturity of the manufacturing process has been demonstrated. A manufacturer or supplier would need to be able to answer all questions below with “YES” in order to deserve the rating “MRL 8”:
- Do manufacturing processes demonstrate acceptable yield and producibility levels for a pilot production line?
- Have all design requirements been satisfied?
- Is the manufacturing process well understood, and subject to 3-Sigma process control, or a comparable quality assessment mechanism?
- As minimal investment in machinery and tooling is the objective, has a demonstration of machinery and tooling been completed in the production environment?
- Are all materials required for production readily available?
- Cost estimates < 125% costing targets (e.g. “design-to-cost” (DTC) targets met for LRIP)?
What is meant by a manufacturing readiness level of 7 (MRL 7)?
A manufacturing readiness level of 7 (MRL 7) generally entails an existing prototype of the manufacturing process. To comply with this rating, an organisation would need to be able to answer all questions quoted below with “YES”:
- Has the prototype system been built on soft tooling, with initial Sigma Levels established?
- Has readiness for low-rate initial production (LRIP) been achieved?
- Is there a significant decrease in required design changes?
- Has process tooling, and inspection and test equipment been demonstrated in the production environment?
- Are the manufacturing processes generally well understood?
- Has the machinery and tooling been proven?
- Have materials been initially demonstrated in production, and have manufacturing processes and procedures been initially demonstrated?
- Have the “design-to-cost” (DTC) targets been validated?
What is indicated by a manufacturing readiness level of 6 (MRL 6)?
A manufacturing readiness level of 6 (MRL 6) generally means that prototyping of critical manufacturing processes has been completed. A manufacturer or supplier would need to be able to answer all of the following questions with “YES” in order to receive this rating:
- Have critical manufacturing processes been prototyped?
- Have targets for improved yield been established?
- Are the process and tooling mature?
- Do design changes still occur frequently?
- Has the investment into machinery and tooling been identified?
- Have quality and reliability levels been identified?
- Have the “design-to-cost” (DTC) identified?
- Has the pilot production line operation been demonstrated?
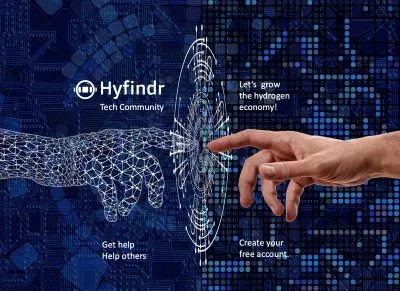
Join the Hyfindr Tech Community
Get help, help others, let us build the hydrogen economy together. No spamming, no marketing, just tech!
What is indicated by a manufacturing readiness level of 5 (MRL 5)?
A manufacturing readiness level of 5 (MRL 5) generally means that a manufacturing process has merely been developed. To be classified under this rating, an organisation would need to answer all questions quoted below with “YES”:
- Have trade studies and laboratory experiments resulted in the development of key manufacturing processes and initial Sigma levels?
- Have preliminary manufacturing assembly sequences been identified?
- Are process, tooling, inspection, and test equipment being developed?
- Are there significant engineering and design changes?
- Have quality and reliability levels not yet been established?
- Has tooling and machinery been demonstrated only in the laboratory?
- Physical and functional interfaces have not been defined in their entirety?
What is inferred by a manufacturing readiness level of 4 or lower?
The MRL classification of 4 or less means that the manufacturing process is not even developed yet. Product listings of MRL level 4 or less are therefore not relevant for the hyfindr.com hydrogen industry marketplace.
The MRL – Manufacturing Readiness Level – is defined in standards designed to allow global comparability of components quality. The well-known DOD Manufacturing Readiness Level deskbook, while originally designed to ascertain regulatory compliance in defense production processes, has become a widely used resource for purposes of TRL MRL levels assessment. Engineers the world over, aiming to achieve the required manufacturing capability readiness level, reference the MRL definitions found in the DOD MRL deskbook in their efforts towards continuous improvement, in order to guarantee business continuity, and to maintain overall operational efficiency. Gaining a thorough understanding of MRL levels and how to achieve them generally yields substantial synergy effects in cost analysis, establishment of effective control systems, and system integration.
Further information can be found at the sources listed below:
Last update: 15.1.2023